Applications of SMC Molding & BMC Molding in Various Industries:
- Electrical: Insulators, switch boxes, electrical equipment enclosures, insulated tools, terminal boards, etc.
- Automotive: Headlamp covers, front and rear bumpers, battery trays, engine soundproofing panels, etc.
- Railway: Vehicle window frames, bathroom components, seats, coffee table tops, carriage sidewalls, and ceilings, etc.
- Construction: Water tanks, bath products, door panels, purification tanks, construction templates, etc.
- Bathroom: Bathtubs, integrated bathroom fixtures, integral molded sinks, etc.
- And various other industrial and agricultural fields.
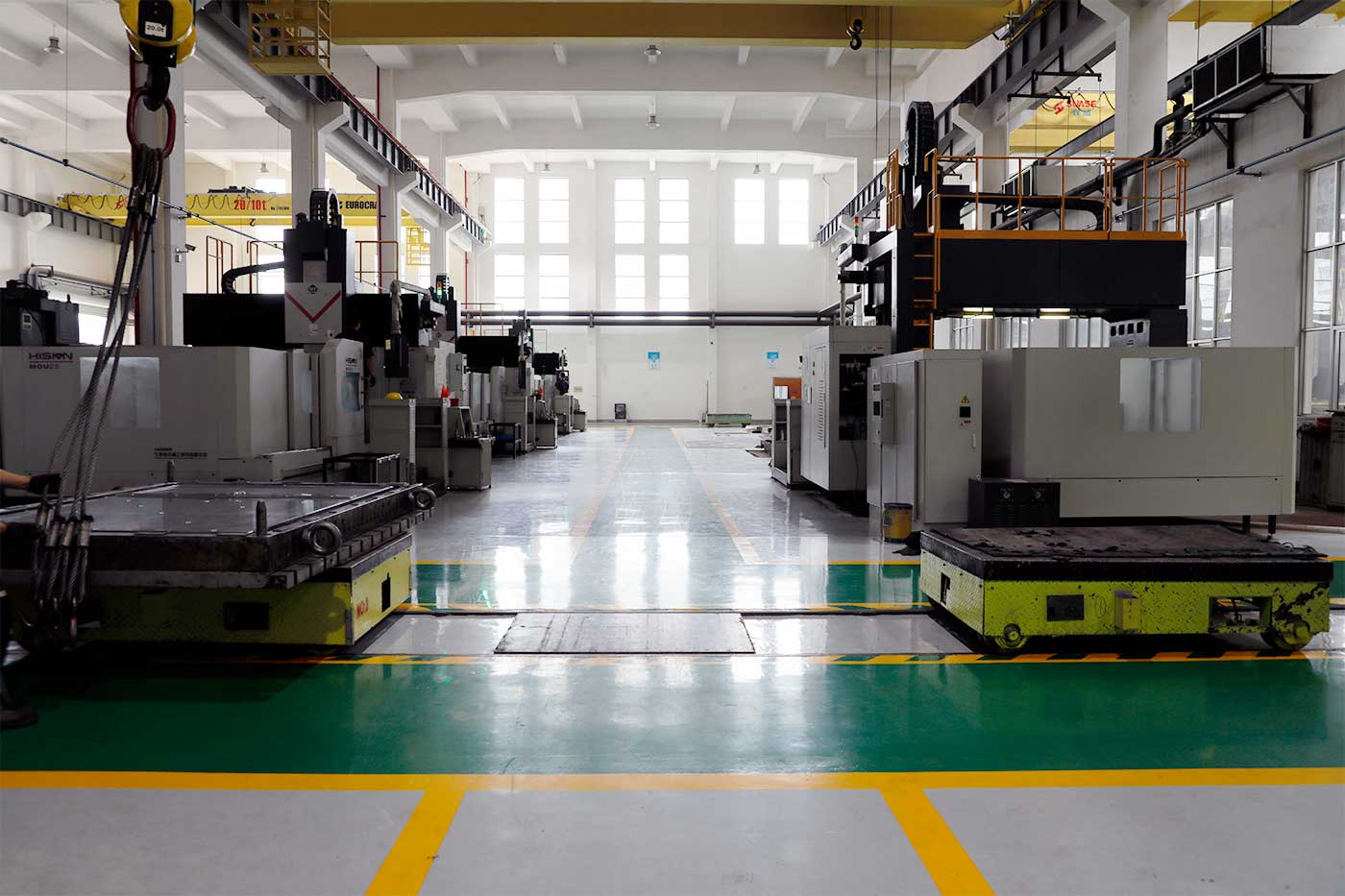
SMC Molding Raw Materials:
SMC materials are composed of GF (special yarn), UP (unsaturated resin), low shrinkage additives, MD (fillers), and various additives.
-
Unsaturated Polyester Resin
- Reacts easily with thickening agents to meet thickening requirements (mainly for SMC).
- Cures rapidly, improving production efficiency.
- Has high heat strength, ensuring that the molded products are not damaged during demolding.
- Provides sufficient toughness to prevent cracking when the component undergoes certain deformations.
-
SMC Tooling
- Safe for storage and operation.
- Does not decompose at room temperature.
- SMC produced with initiators has a long storage life and rapidly decomposes and cross-links at elevated temperatures.
- Cost-effective.
-
Anti-agglomerants
Prevent unsaturated polyester resin from crosslinking polymerization at room temperature, extending the storage life.
-
Thickening Agents
SMC requires high viscosity during compression molding, storage, and transportation. Thickening agents are used to achieve this.
Selection Criteria:
- Low viscosity is required during preparation to ensure thorough impregnation of resin into glass fibers and fillers.
- After impregnation, viscosity should increase rapidly to adapt to storage, transportation, and molding operations.
- Thickened blanks should quickly fill the mold cavity at molding temperatures and prevent resin-fiber separation.
- Viscosity after thickening should remain stable within the moldable range during the storage period.
- Thickening effect should be reproducible consistently during production.
-
Low Shrinkage Additives
General polyester resins have a curing shrinkage rate of 7% to 10%. Adding low shrinkage additives can significantly reduce the shrinkage rate, making it close to zero. It also ensures smooth, ripple-free surfaces of SMC products.
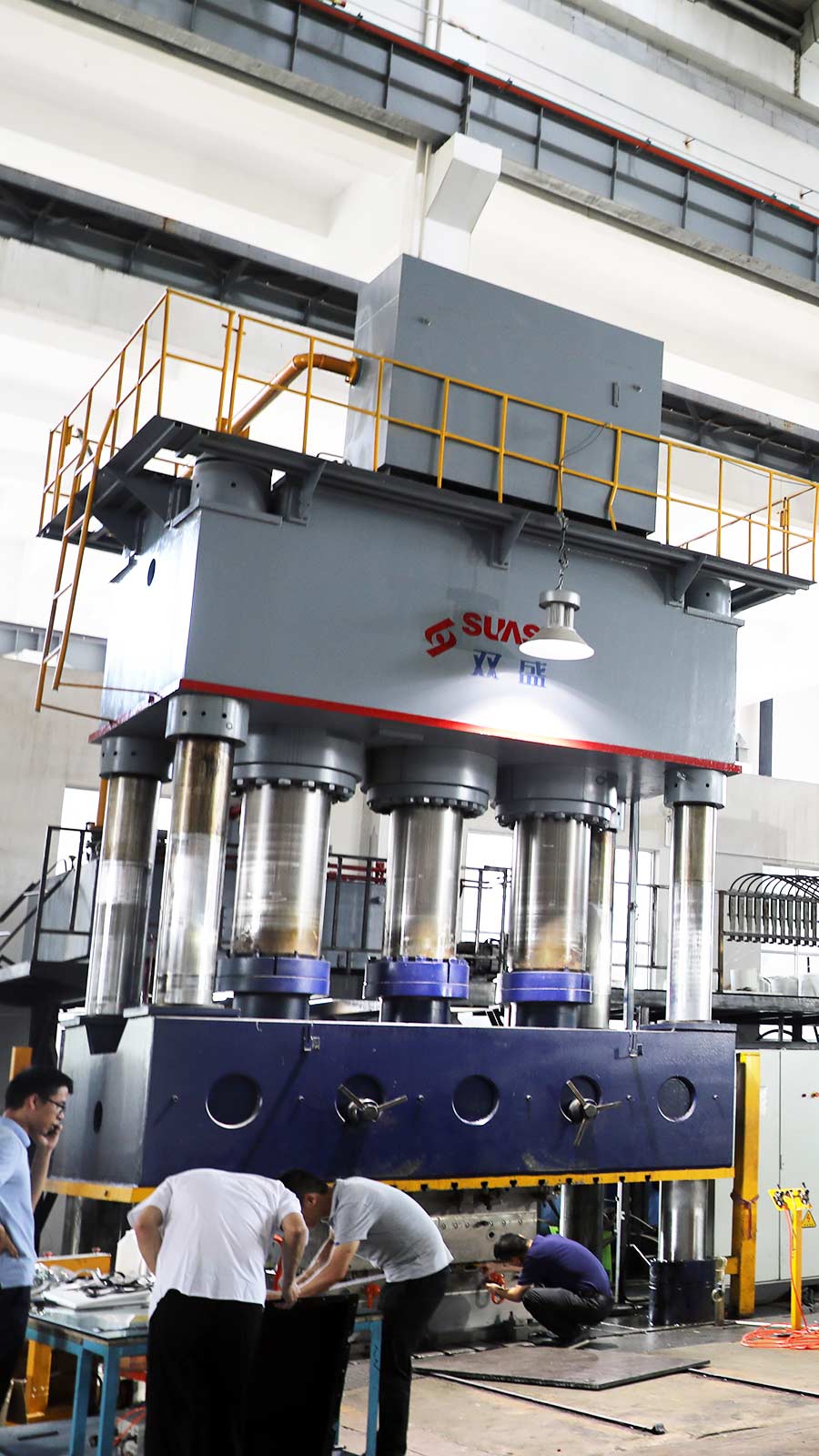