BMC Mold Design & Manufacturing: High-Performance Thermoset Compression Molding Solutions
- Suase /
- SUASE NEWS
What is a BMC Mold?
BMC mold is a thermoset compression mold specifically designed for forming BMC (Bulk Molding Compound) materials. BMC is a premixed glass fiber-reinforced thermoset resin composite, widely used in electrical insulation, automotive components, construction elements, and more. BMC molds typically use rigid metal structures that can withstand high-temperature and high-pressure environments to achieve high-precision molding of complex parts.
Material Properties of BMC Determine Mold Structure
The characteristics of BMC materials directly influence mold design:
- High flowability, suitable for molding complex shapes
- Thermosetting property, non-recyclable after molding
- Excellent electrical insulation and heat resistance
- High glass fiber content, requiring strong mold wear resistance
Therefore, BMC molds must be designed for high precision, wear resistance, effective venting systems, and high-temperature thermal control.
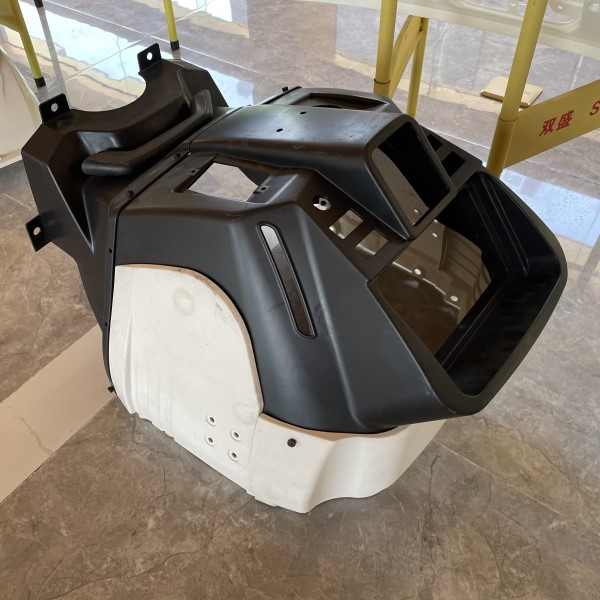
Key Considerations in BMC Mold Design
- Mold Cavity Design: Precisely match product dimensions and control shrinkage rate.
- Venting System: BMC releases gases during molding, so effective venting grooves must be designed to avoid air pockets.
- Heating System: Typically uses electric or oil heating, controlled at 130–170°C.
- Demolding Structure: Due to the high strength of BMC parts, components like lifters, ejector pins, and compound demolding mechanisms are needed.
- Wear Resistance Treatment: Cavity surfaces can be treated with nitriding, chrome plating, PVD, etc., to extend mold life.
BMC Mold Manufacturing Process
High-quality BMC molds require advanced manufacturing technologies, such as:
- Precision CNC machining and Electrical Discharge Machining (EDM)
- High-speed milling for complex geometries
- Mold surface polishing and fine finishing to enhance product appearance
- Selection of high-hardness steels like P20, 2738, H13, etc.
The typical service life of BMC molds ranges from 50,000 to 300,000 molding cycles, depending on steel grade and machining precision.
Typical Application Areas
BMC molds are widely used in high-performance industries:
- Electrical Industry: Distribution box housings, meter covers, insulators, low-voltage switch shells
- Automotive Industry: Headlamp brackets, fuse boxes, battery housings, electronic module brackets
- Home Appliances: Washing machine motor end covers, fan bases, heater housings
- Construction & Sanitary Ware: SMC/BMC washbasin bases, toilet covers, bathtub rims
Difference from SMC Molds
Although SMC (Sheet Molding Compound) and BMC are both thermoset molding compounds, their molds differ in design:
Item | BMC Mold | SMC Mold |
---|---|---|
Material Form | Paste or dough-like | Sheet |
Molding Method | Injection-compression or charge compression | Lay-up and compression |
Venting Design | More complex, more gas | Relatively simple |
Suitable Products | Small to medium-sized precision parts | Large structural components |
Trends in BMC Mold Development
With the rise of new energy vehicles, smart grids, and green building materials, BMC molds are evolving toward:
- Highly integrated molds supporting insert molding of functional parts
- Multi-cavity structures to improve production efficiency
- Digital mold flow analysis to optimize feeding and venting
- Integration with automated compression molding lines for consistent quality
Importance of Choosing a Reliable BMC Mold Supplier
A qualified BMC mold manufacturer should possess mold flow analysis capabilities, experience in automated design, and a strict quality control system. High-quality molds not only improve molding efficiency but also reduce defective rates and maintenance costs.
If you are looking for a partner to undertake custom BMC mold design, mass production mold manufacturing, or compression molding process optimization, we recommend choosing a manufacturer with extensive industry experience.
This article aims to provide comprehensive technical insights into BMC molds. For specific mold quotations, material recommendations, or sample support, feel free to contact our engineering team.
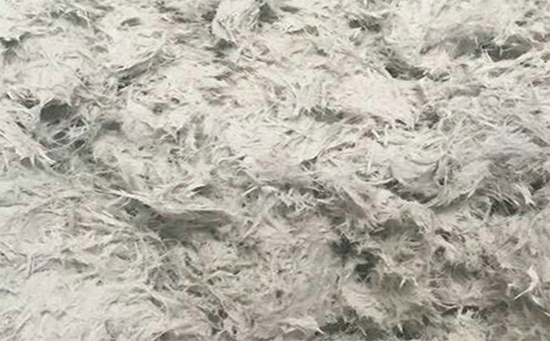